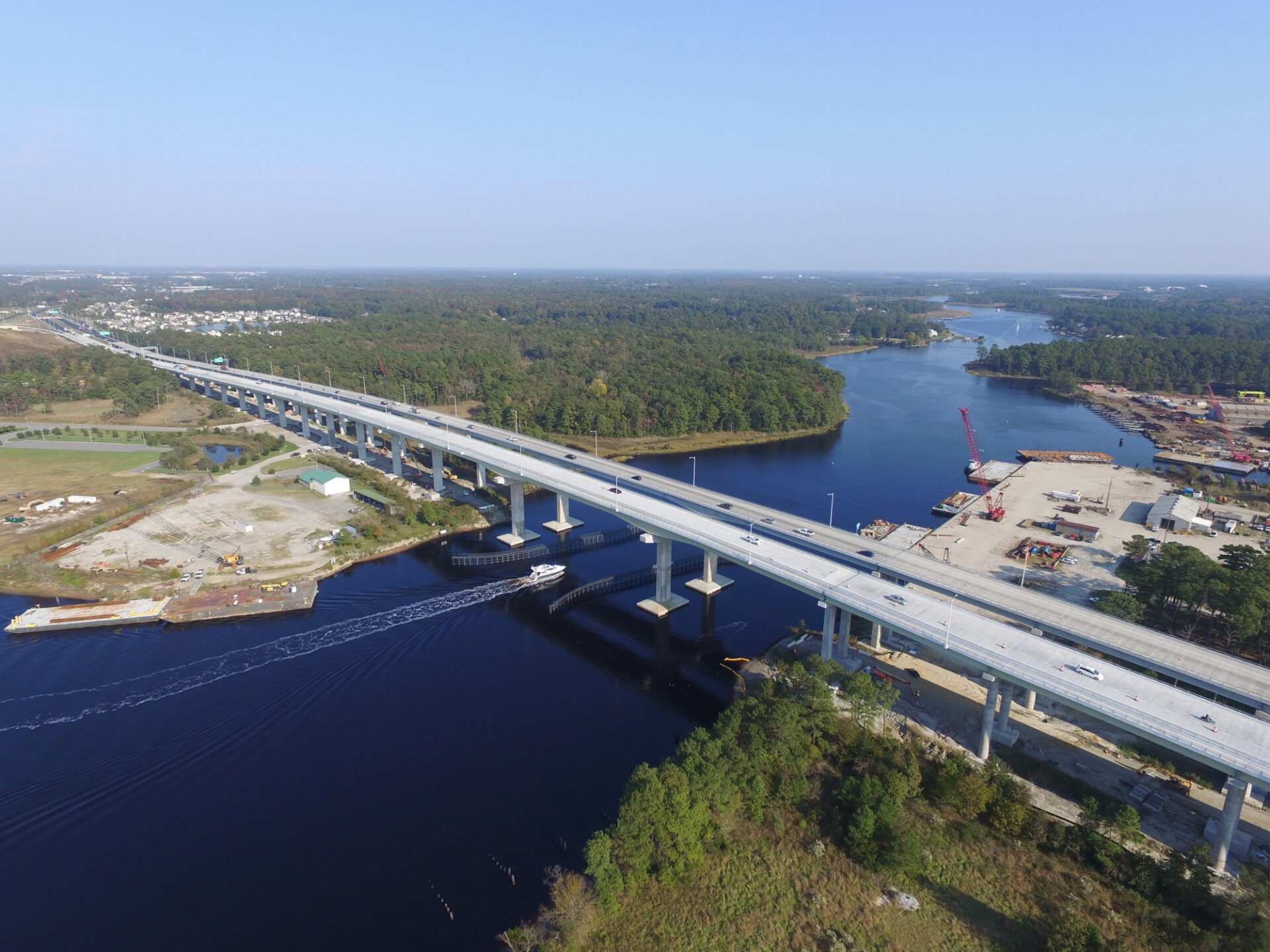
City of Chesapeake, Dominion Boulevard Improvements
Chesapeake, VA
Dominion Boulevard/U.S. Route 17 in Chesapeake, Virginia, was once labeled a safety hazard. Unbeknownst to most commuters traveling the 3.8-mile corridor, the accident rate was the highest in the region. The existing two-lane roadway and steel drawbridge could not accommodate traffic demands and delays resulting from an average of 16 bridge lifts per day (nearly 6,000 per year). Rated by Congress as one of 20 National Highway System High Priority Corridors, the route was also a designated hurricane evacuation route and was prone to flooding.
Challenge
Despite the pressing need for improvements, a lack of sufficient funding hampered efforts to move the project forward. Eventually, the city chose to find its own solution and pursued the work as a Virginia Department of Transportation (VDOT) locally administered project (LAP), in which the local government would ultimately manage the project with oversight from VDOT.
Upon approval, the Dominion Boulevard project became the largest VDOT LAP in Virginia history, with the City of Chesapeake opting to replace the two-lane drawbridge built in 1964 with two parallel two-lane fixed span bridges, 95-foot high over the Elizabeth River in order to eliminate the need for bridge openings and the stop-and-go traffic causing the majority of the accidents along the corridor. The City additionally sought to widen the entire four-mile corridor from two to four lanes which included three new interchanges and nine bridges. A fully-automated toll collection system was also planned with state-of-the-art open road tolling technology.
MBP was brought on by the City of Chesapeake to provide construction management and inspection services. Under the requirements of a LAP project, MBP was challenged to provide a more comprehensive construction management program than required by a traditional VDOT-administered project. Included with these additional responsibilities was the need to implement a quality control program that involved both on-site inspections and off-site plant inspections occurring in four different states.
Solution
Due to the complexity of this project, MBP immediately implemented an integrated Project Risk Management program, which brought together all key stakeholders including the owner, designer, and contractors to resolve potential issues and avoid impacts to the schedule and budget ahead of time. In order to manage the over 1,000 different unit price pay items on this project – the largest known number on any project in Virginia – MBP developed a customized web-based project controls system for collaboration with the entire project team. This site enabled internet access to project documents, expedited the review of over 700 submittals and 650 requests for information, and avoided project delays due to the review process. MBP’s site allowed for the streamlined flow of information amongst the project team. At any given time, the project team had instant access to the latest cloud-based information, and received automatic notifications when information was updated. Information sharing was completely seamless and effective.
Under a change to MBP’s scope during construction, the City requested that MBP manage a second, adjacent project accomplishing the City’s goal of completing both projects at the same time. MBP worked with the City and designer to implement temporary work zone traffic patterns to eliminate any conflicts between the two adjacent projects. MBP also worked with the City to adjust the design and project limits to economically accommodate the second project, including eliminating over $300,000 of temporary construction that would have otherwise been required.
The implementation of the automated, state-of-the-art open-road toll collection system, a free-flowing toll collection system without the use of toll booths, stood for a unique challenge. For this system, all tolling data had to be collected solely from overhead devices, which is only accomplished in very few locations throughout the country. Ensuring that the system would function as intended required extensive coordination throughout the submittal process to refine the scope and achieve the City’s expectations. MBP’s staff oversaw the factory acceptance testing of the proposed tolling system at an off-site simulated facility, and then continued to manage the site integration and acceptance testing in conjunction with the contractor’s tolling vendor. When the entire tolling system was activated, the toll-collection system was essentially flawless.
Result
All new lanes of traffic were opened 111 days prior to the original contract completion date, to the great satisfaction of both commuters and the City of Chesapeake. Another key milestone was the activation of the open-road tolling system 40 days ahead of the original contract completion date. This key early achievement enabled the City to begin collecting toll revenue ahead of the planned financial projections. With nine bridges, two rising 95 feet above the river, and maintaining traffic on this heavily traveled corridor, the project team identified fall protection and work zone safety as significant safety risks. Dominion Boulevard Constructors (DBC, the general contractor joint venture) worked nearly 950,000 man hours during the project without any injuries related to falls or work zone incidents.
Through bi-weekly risk mitigation strategy sessions, all potential risks were successfully mitigated without impacting the project completion date. Based on the project team’s assessment of the potential risks, in total there were over $8 million of potential risks that were mitigated, and over 300 days of project impacts that were avoided. The solutions to some of these potential issues resulted in additional cost savings to the owner through modifications of originally planned work. Overall, the project team identified over $4 million in cost savings through a combination of value engineering initiatives and other scope changes.
“With your help we made history. The project was delivered not only on-time and within budget, but it was also the largest project the city has ever undertaken and the largest locally administered project in the history of the Commonwealth of Virginia. After four years of construction, after building nine bridges, one of the most important things to us and the city is that everybody went home at the end of this project. That’s truly a testament to your management, to your emphasis on safety, and to all the hard work that you and your staff did. I thank you for all that work and look forward to working with you on future projects here in the City of Chesapeake.”
Earl Sorey, PE
Assistant Director of Public Works
City of Chesapeake
Featured in the News
Creative Solutions Make Needed Chesapeake Bridge a Reality
Read more at ENR
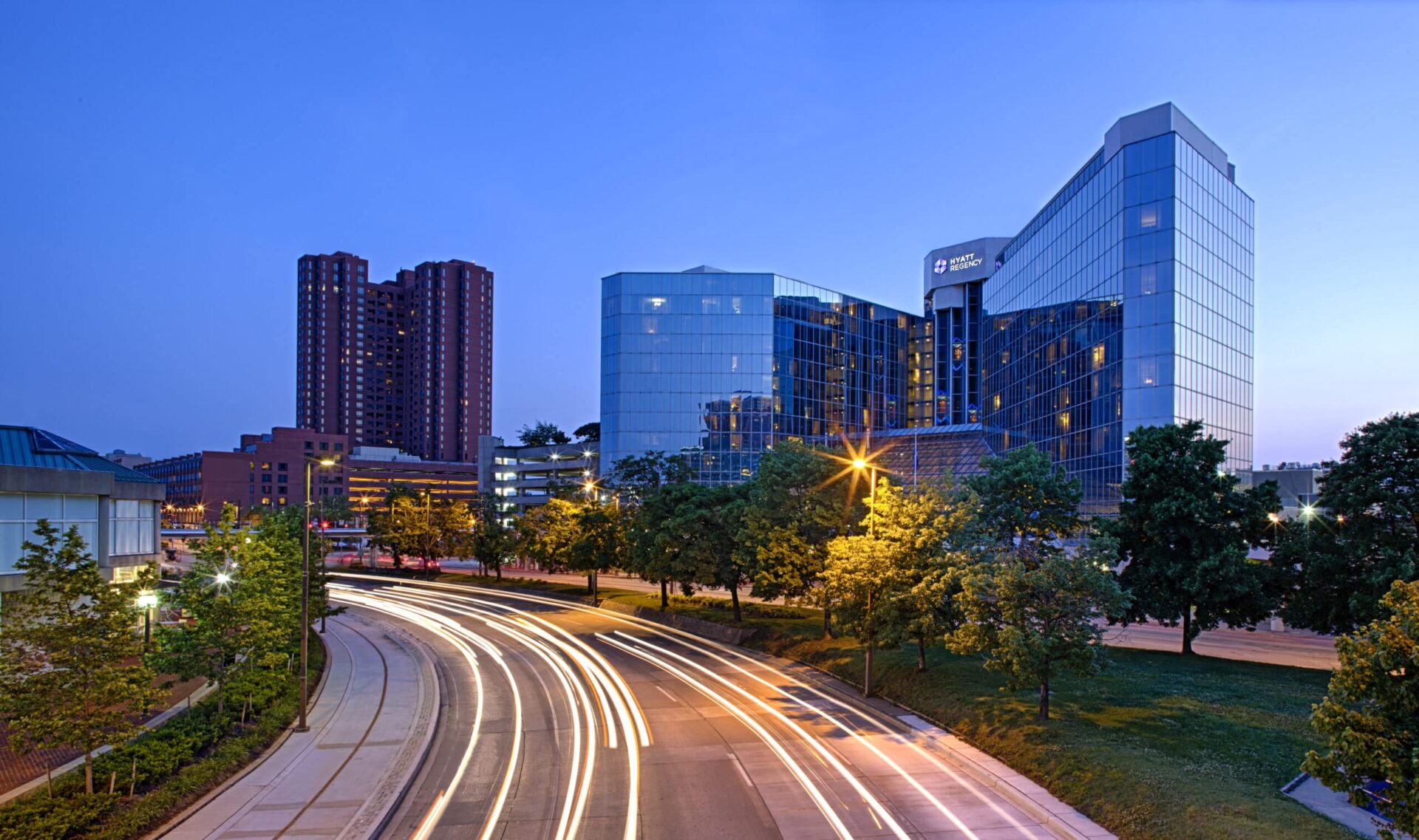
Explore Our Blog
Stay informed with the latest insights, lessons learned, and thought leadership from MBP’s experts.
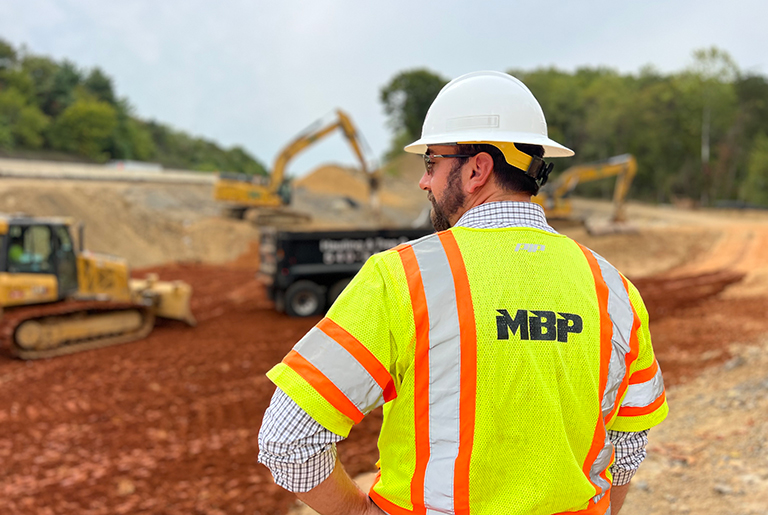
Be a Part of Something Great
At MBP, you’ll be part of a supportive, collaborative environment where your skills are valued, your growth is prioritized, and your work makes a real impact.