Facility departments are faced with an overwhelming amount of data regarding the condition of their buildings. Typical building automation systems (BAS) produce more data points and generate more automated alarms than a facilities department can realistically view and manage, which often results in information overload. Simply having access to facility data does not easily translate to reducing energy consumption, achieving energy savings, and extending equipment lifespan. To add to this, the complexity of BAS sequences has made it increasingly difficult to prioritize efforts, and automated alarms often get ignored because of sheer volume.
MBCx can change all of that.
What is Monitoring-Based Commissioning?
The U.S. Green Building Council (USGBC) defines MBCx as providing “the building owner, operators, and the commissioning authority a continual stream of information that helps them identify operational issues as they occur, thereby saving time, money, and energy consumption over the lifetime of the building.” Recognizing the value of MBCx, USGBC has incorporated it into the LEED version 4 certification process.
MBCx allows facility owners to evaluate the performance of their building systems in real-time by accessing and analyzing millions of data points streaming through a facility and producing a scoring system that ranks equipment based on performance. Through a cloud-based tool, facility owners see trends in energy use, diagnose problems, and discover savings opportunities both immediately and long term.
My BAS already has alarms programmed, so why would I need MBCx?
I think of MBCx as a glimpse into the future of building performance. While BAS have analytics that set off alarms when there are issues, they are typically not the most efficient way of setting priorities.
Recently, I visited a facilities manager at a community college who walked me through his BAS. He was so excited about its capabilities that he pulled up a couple of chairs in front of his computer, opened the BAS interface, and showed me a building floor plan with each room shown in green. “See,” he said, “I now know this building is maintaining space conditions and doesn’t have any significant issues so I can go to the next building.” After closing the first screen he then selected another building and we waited for the screen to load. For the second building, all the spaces were shown in green and one space was shown in red. “Ah! Now I know there is an issue in that space.” He then clicked the screen and we waited again for the room graphic to open. “Here I can see the VAV box and look at the discharge temp, airflow, and control valve. If it looks like this is working per design, then I can trace it back to the air handler.” Again, he clicked another window and we waited for the screen to load. He proceeded to flip through screen after screen looking at the chiller plant, pumps, cooling towers, etc. until finally, he said, “I take all the issues identified through this process and this is how I develop my work orders for the day.”
I thought to myself that this seemed so much harder than it had to be.
How does MBCx help facility managers focus their time and set priorities?
After sitting side by side with this facility manager for some time, I asked him how long it takes him to do this every day. He replied, “Usually about three or four hours.”
Again, I thought, that is way too long.
Facility managers have a lot on their plates. They really do not have the luxury of spending three to four hours a day hunting for issues for their crews to go and resolve. Typically, operations and maintenance (O&M) crews are limited and spend much of their time chasing hot/cold calls and treating the symptoms of the underlying systemic problems. They need a way to quickly identify and prioritize system problems and solutions on a daily basis.
Implementing MBCx would allow this facility manager to sit down in the morning with his cup of coffee, open one screen, and instantly see the top ten poorest performing devices on his campus before developing his work orders for the day. With his limited crew, perhaps he doesn’t want to send them all over campus to address one device in one building and two devices in another building, etc. MBCx allows him to rank the performance of all his buildings by finding the worst performing building and focusing his efforts on resolving the devices in that building that are contributing to the unacceptable performance score.
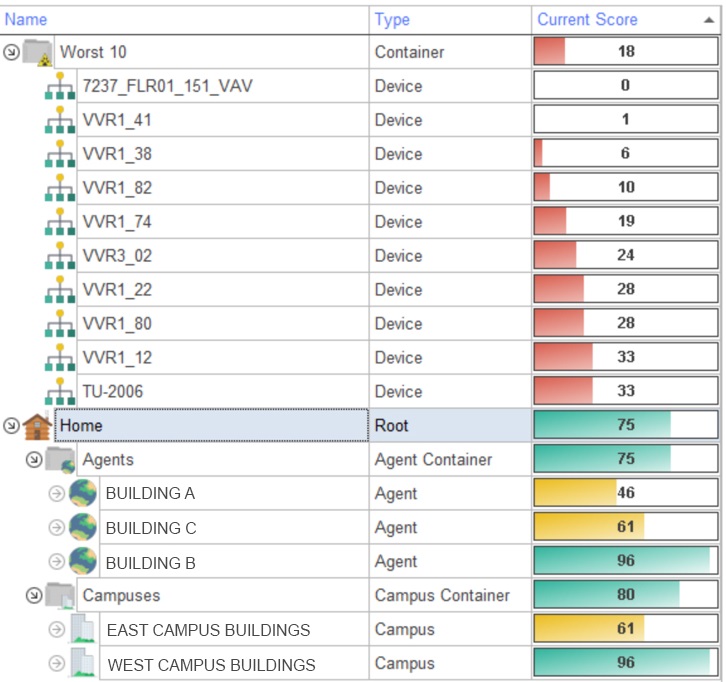
MBCx lets you instantly prioritize O&M per campus, building, and/or device level
So where are the cost savings?
MBCx provides the opportunity to improve operational efficiency by reducing the time needed to identify issues and helping to develop work orders in a fraction of time. The facility manager at the community college that I met with could benefit from saving at least two hours per day (25%). When more complex issues are identified, MBCx can often save up to eight hours of troubleshooting time by eliminating the need to run trend reports and convert them into Excel PowerPivot files to complete trend analysis. In addition, many issues can be identified remotely through analytics reducing visual inspections that may be delayed due to space occupancy or be time intensive due to accessibility (such as requiring a lift to get to equipment located above high ceilings).
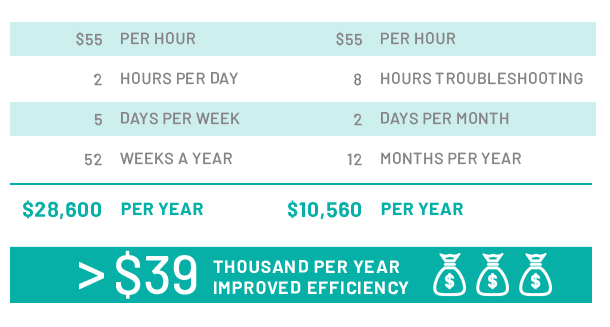
All told, this could improve the operational efficiency of the facility manager by nearly $40,000 per year, and that does not include the additional system performance improvements that can be made with the two hours per day the facility manager now has back. By focusing on those buildings that need the most attention first, the facility manager can gradually get systems operating closer to original designed efficiency (reducing wasted energy costs), allowing the O&M staff to actually maintain their facilities, rather than simply chasing hot and cold calls.
While the value of MBCx is often presented as energy savings, in reality, the true value of MBCx is much more than saving energy. Implementation of MBCx has the potential to save facility managers over 25% in operational efficiency.
If you are looking to optimize your facility’s performance, learn more about MBP’s facility performance consulting services, and contact us when you’re ready to improve your operational efficiency.