“What do you do when your switchgear is lost in the mail?”
That was the question posed to a panel of experts to provoke a conversation about the state of today’s supply chain at this year’s Associated General Contractors (AGC) 2023 Surety Bonding and Construction Risk Management Conference. I was honored to moderate the panel, which consisted of an owner, a contractor, an attorney, and a surety representative. The group agreed that several factors—lack of labor resources, geo-political struggles, and scarcity of raw materials—are driving supply chain volatility and vulnerability and it shows no signs of relenting.
According to a November 15, 2022, New York Times article, “For the Want of an Insulation Screw,” switchgear, the electronics control systems at the center of every building, requires the same chips used in auto production, leading to shortages as the two industries compete for them. Switchgear is not the only item missing from the backs of trucks either. In the latest AGC survey, “Buy America Material,” 70% of respondents indicated that they are waiting longer than expected for structural steel, steel mesh, plate steel, steel pipe, copper products, aluminum products, plastics and polymers, plumbing fixtures, precast concrete products, HVAC system, water pumps, electrical equipment, and windows.
And, exactly what is “longer than expected?” Days, weeks, or months?
In an article for the Seattle Daily Journal of Commerce, The new holy grail for general contractors: nailing down lead times for key components, a contractor said, “certain equipment including switchgear, air-cooled chillers, and backup generators may need to be purchased 18 to 24 months in advance of the need date.” The contractor continued that “[if] project teams do not have this amount of time, they need to look at resequencing work and come up with temporary power or cooling measures in order to work around the permanent deliveries, which can be challenging.”
Material Pricing Challenges
Another challenge has been the volatility of material pricing. According to the U.S. Bureau of Labor Statistics, softwood lumber experienced two separate pricing spikes in 2021 and 2022, with extreme fluctuations. As seen in Figure 1, taken from the U.S. Bureau of Labor Statistics website, the first spike occurred in May 2021, with prices increasing 161.35% from the previous May, dropping 112.3% in August 2021, increasing 97.5% in March 2022, and then dropping 201.6% in January 2023, which is still 16.7% more than pre-COVID-19 pricing.
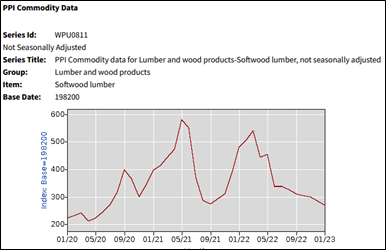
Even though softwood lumber pricing has closely returned to pre-COVID-19 pricing, concrete pipe pricing increased by approximately 22.5% from January 2022 to January 2023, as shown in Figure 2.
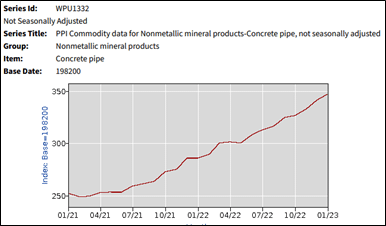
These two pricing examples, and the lagging availability of manufactured materials, demonstrate the volatility that both contractors and owners have encountered and continue to encounter, creating risk for the overall construction industry.
Industry Responses to Challenges
In the panel discussion at the AGC Conference, each representative presented their perspective on addressing the challenges.
The contractor on the panel said that the availability of subcontractor resources (capital, material, labor, and equipment) weighs most heavily on his mind considering present-day supply chain pressure. Subcontractor capacity is crushing, he noted, with most contractors settling on their third and fourth choice when picking subcontractors for jobs. Working with unfamiliar subcontractors creates a risk that sometimes outweighs the benefits. In fact, the contractor on the panel confessed that he sometimes must make the tough decision and take a pass on the contract.
To soften the blow of battered supply chains, the attorney on the panel offered the opportunity for flexibility with contracts and contracting language. For example, he presented the option to insert a contract clause of potential applicability, i.e., supply chain disruption and material/price escalators. Another possible method of addressing the risk, he suggested, was the use of Force Majeure clauses for remedy, where the contract may identify a variety of man-made events, like AIA A201-2017 General Conditions, Section 8, which addresses time extensions due to “unusual delay in deliveries.”
The surety representative had the unfortunate position at the table of being without contractual signature authority, but with a possible financial responsibility to complete the contract in the event a contractor or subcontractor fails to perform. The surety representative indicated that the entity calling the bond must be educated that the surety likely will not be able to overcome the supply chain volatility, which may cause further delay.
Contractors need to communicate to owners the volatility of the potential supply chain risks they may encounter as soon as possible. As the attorney suggested, contract language is available that creates shared risk between the owner and contractor in defined periods of escalation or supply chain issues. However, as the owner representative on the panel highlighted, contractors must not forget that a certain level of risk is placed on the contractor for these issues as defined by the contract. With that said, the owner acknowledged that ultimately, if escalation or supply chain disruptions cause an issue on its project, the owner suffers with the delayed delivery of its completed facility. Unlike the past when supply chain risks were likely to have little effect on project duration, owners and contractors (and subcontractors) must now remain diligent with their communication but also with their market condition research as part of their project risk assessment.
Final Word
From my experience of moderating this panel of experts, it became apparent that collaboration is essential to address the challenges with the supply chain and other resource volatility facing the construction industry. These include:
- Contractors working closely with subcontractors and vendors to understand performance and delivery risks on the project,
- All parties proactively addressing risk sharing and risk bearing as defined in contract language, and
- Contractors and owners sharing up-to-date information on risks of material and equipment availability and pricing both during procurement and construction periods.
A more detailed overview of our AGC panel discussion can be found in our paper, What To Do When Your Switchgear Is Lost in the Mail – a Panel Discussion on Supply Chain Risk Management, here.