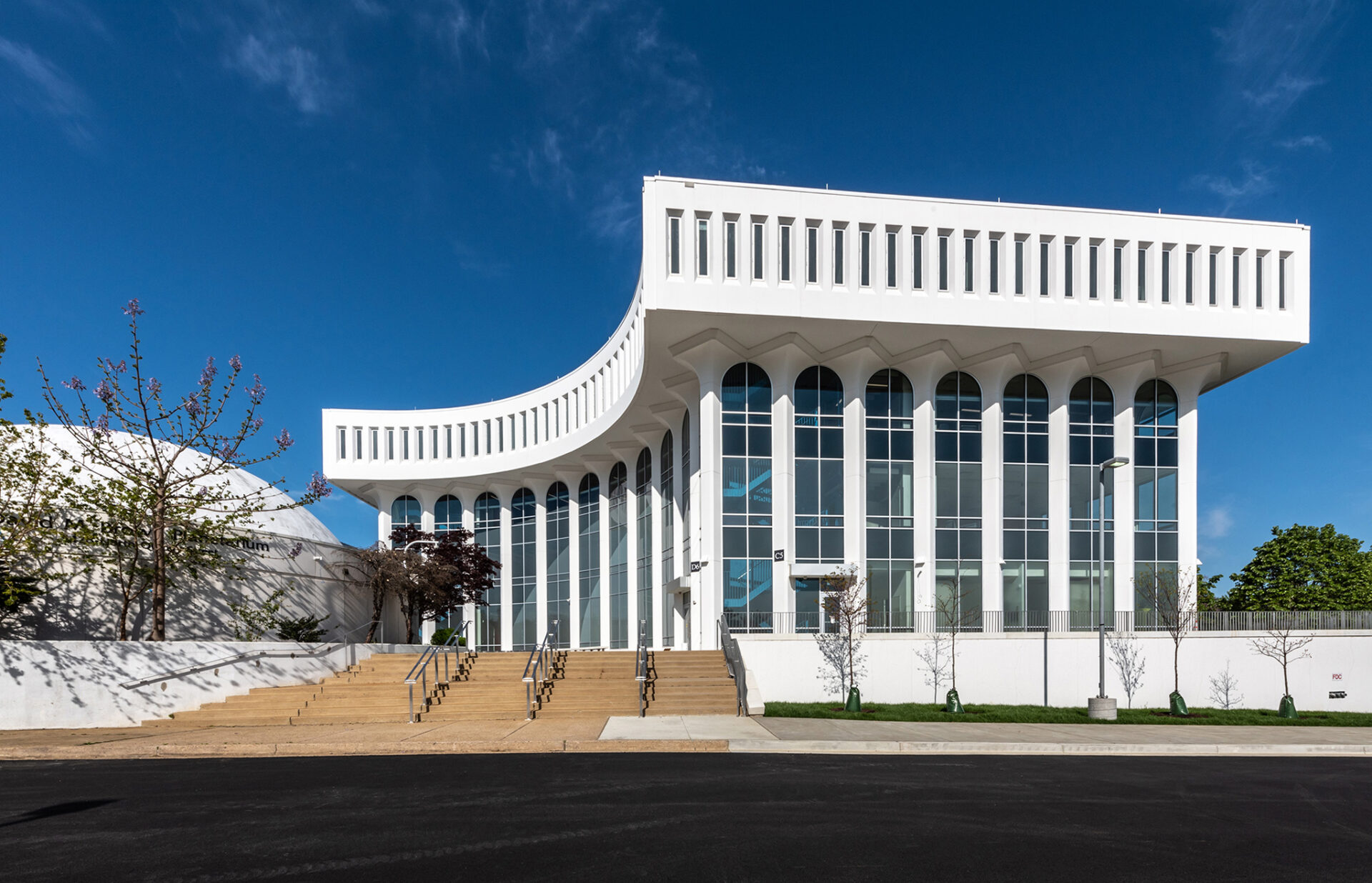
Arlington Public Schools, Education Center Reuse
Arlington, VA
In order to meet the demands of the growing Arlington County community, Arlington Public Schools (APS) needed to find a way to expand Washington-Liberty High School. The answer? The Education Center Reuse project. APS planned on converting their previous headquarters building for use as an annex to the high school. The new space would provide an array of new teaching spaces including science classrooms, a chemistry lab, art rooms, general classrooms, PE space, and the capacity to accommodate 600 additional students. Not only would this new building provide the needed space, but ultimately the feel of a college campus environment.
Challenge
When APS awarded MBP the Construction Administration Services task order for the Education Center Reuse Project, we began to consider new project management techniques that could augment the level of service MBP was to provide to APS.
The Education Center Reuse project was valued at $25.6 million in direct construction costs and would include the renovation of an existing two-and-a-half-acre campus that housed a curved, five-story, 55,169-square-foot building with a detached planetarium.
The unique Education Center Reuse building posed several challenges for the project team. Since the project included both significant exterior and interior renovations, the foremost challenge was how the limited project team was to document construction progress regularly and meaningfully. Additionally, given the condensed 12-month construction schedule proposed by the Construction Manager at Risk (CMaR), MBP had to consider how it was going to positively affect conversations to ensure quick access to information so that the owner team could make timely project decisions.
Solution
Considering the magnitude of these challenges, MBP needed to consider how to augment traditional project management strategies with new, digital construction methods that would help the owner complete the project on time and within budget. Accordingly, MBP decided to focus on developing digital construction strategies underpinned by the paradigms of improving accessibility and reducing project risk. After working with the owner team to determine key areas of risk, the MBP team decided to focus on developing a system that could allow easy access to existing conditions as well as up-to-date project conditions. With access to this information, MBP projected that the request for information (RFI), submittal review, change management, and scheduling processes could all be positively impacted.
To implement this new digital construction strategy, the MBP team evaluated several options including various PMIS systems, virtual capture technologies, and MBP self-created innovations. Ultimately, the team decided to implement a virtual capture platform. The platform, which utilizes a series of 360-degree images, organized by geographical location to document overall construction progress, was both portable and collaborative. After piloting the platform on another project, the program was rolled out on the Education Center Reuse project.
When the MBP team began implementing 360-capture on the project, it quickly became apparent that to accomplish the goals of the strategy, the team needed to ensure that there was robust photo coverage of the project site. Building from that idea, the team worked with the rest of the owner project team members to develop a coverage plan for various capture locations. These locations included each room in the building, key points of coordination concern, as well as vantage points that showed notable site, building, and room features. To validate the coverage, a series of 360 photos were taken throughout the space, and after several iterations, the coverage was refined, and estimated to show roughly 93% of the project site and building.
After setting these capture locations, the project team set up a regular process for marking the points, capturing the points, and reviewing the points to ensure consistency and quality. After a couple of weeks of use, access to the platform was provided to the owner project team. In parallel, the MBP team started weaving it into normal project correspondence. Though not adopted without some opportunities for improvement, 360-capture quickly became the go-to resource for evaluating RFI responses, existing condition variations, coordination of new systems with the existing structure, and other progress of construction change orders and time extension claims.
The team utilized several tools within the platform to highlight, memorialize, and categorize various occurrences on the project to augment the accessibility of contemporaneous data. By converting these image markups into digital tables, the MBP team was able to easily integrate project workflows, which led to the team having more accurate and interactive risk registers, as-built schedule reviews, RFI responses, change order responses, quality control reports, and weekly project team progress meetings. The presentation of this data in a sortable, interactive manner provided APS and the owner team with not only more accessibility to real-time analytics and data with which to make decisions but also more robust and defensible risk registers, CMaR and subcontractor monthly billing reviews, as-built schedule reviews, and daily reports.
Result
Although the positive results were apparent from the outset of implementing 360-capture as part of MBP’s digital construction strategy on this project, they were intangible at first as the benefits related more to owner-team processes than easily perceived value. It was proven that the team could do more in less time, however, that benefit was hard to quantify with a high degree of certainty. As such, the MBP team looked for other options to evaluate the return on investment (ROI) of the 360-capture tool to APS.
The adoption of HoloBuilder for responding to RFIs was noted numerous times on the project, however, a notable instance of its use came in the form of one of the design team subconsultant’s project memos. This subconsultant utilized the 360-capture platform to evaluate a design challenge without having to visit the project site. As this site visit and site visits from other owner team members are generally limited in quantity on the project, the ability to perform a defensible evaluation of the challenge virtually afforded APS the opportunity to save on the cost of the site visit. In this instance, the savings was nearly $1,100. Though only one example of this occurrence, it is reasonable to compare these savings to the direct cost of a 360-capture license. This means that after only four saved extra site visits on the project, an owner could recoup the entire license fee and MBP’s associated capture time.
Though implementing a new digital construction strategy on a project initially appeared daunting to the MBP project team, it proved to be an immediate and impactful benefit to the project and owner teams. MBP was able to assist APS in providing not only a new tool but also implementing it in an organized, consistent, and easily understood manner.
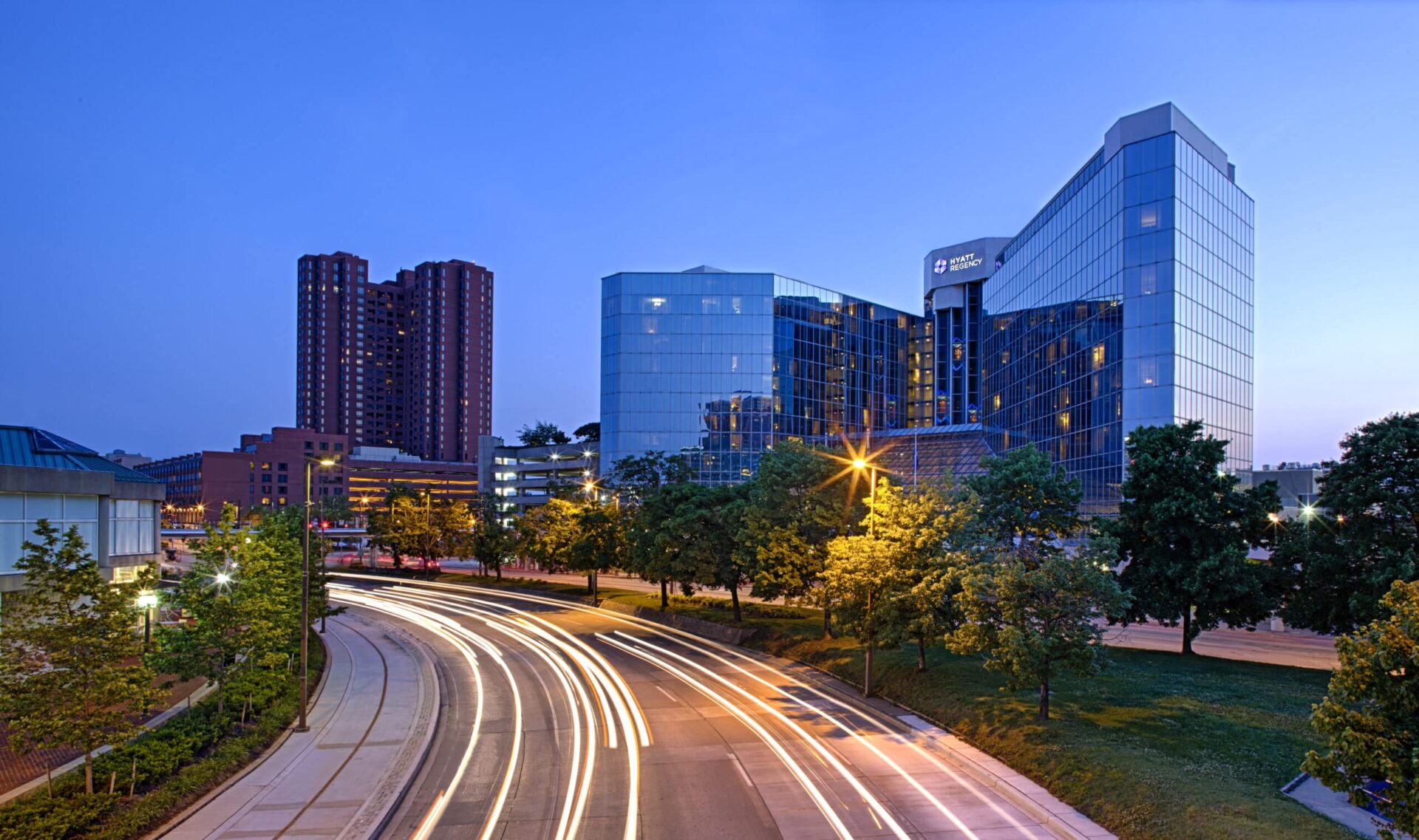
Explore Our Blog
Stay informed with the latest insights, lessons learned, and thought leadership from MBP’s experts.
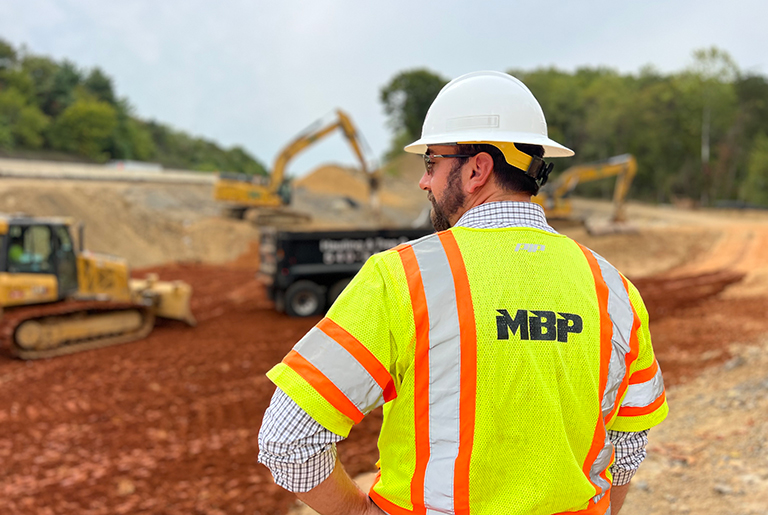
Be a Part of Something Great
At MBP, you’ll be part of a supportive, collaborative environment where your skills are valued, your growth is prioritized, and your work makes a real impact.